
In the event you’ve been hanging round on the planet of electrical bikes for any first rate period of time, you’ve most likely come throughout Bafang. They don’t make electrical bikes, however they’ve lengthy made most of the parts utilized by them. I visited the manufacturing facility again in 2019, and lately returned for a second go to to see what had modified. Boy, was I unprepared for what awaited me…
After I say that Bafang makes most of the parts discovered within the e-bike you most likely have at dwelling, that now looks like an understatement. With all the new tech and developments the corporate has made, they now produce nearly each half utilized in electrical bike drive methods.
And never solely that, however their manufacturing processes have modified considerably over the previous couple of years.
To see behind the scenes your self, try my video from the go to under.
Even from the primary second I walked by means of the gates, the updates have been obvious. Since my final go to, Bafang has moved into an enormous new complicated, which is necessary since a few of their new manufacturing now contains the addition of full e-bike battery design and manufacturing. That clearly requires considerably extra of a footprint than only a motor and drive system maker.
However earlier than I get to the brand new battery work, let’s begin at the start. I started my go to within the R&D division, the place a devoted crew of engineers and designers work collectively on drawing up the subsequent technology of e-bike parts. After I visited in 2019, there have been hints within the air that Bafang was engaged on an answer to the widespread problem of e-bike motors having an unlucky tendency to wreak havoc on conventional bicycle transmissions. There’s only a restricted quantity of energy that almost all bicycle shifters and derailleurs are designed for, and that quantity normally falls above leg energy however under motor energy.
Now I used to be happy to see that Bafang has a number of choices for their very own in-house developed transmissions constructed round internally geared hubs (IGHs). IGHs are prized within the bicycle world for his or her clear, low-maintenance design that utterly replaces a dangling derailleur. Nevertheless, using an internally geared hub typically means you may’t use a hub motor (or must put it within the entrance wheel, which is much less fascinating). However not solely has Bafang developed their very own IGHs, however they’ve even included hub motors into the design, creating multi-speed transmissions that share the identical wheel hub as an electrical motor. That innovation, often called the Bafang GVT line (Gear Variable Transmission), opens an entire new world of e-bike potentialities by placing an internally geared hub and a hub motor in the identical product. And on high of that, the shifting happens fully mechanically and with out exterior cables or wires. Intelligent use of mechanical parts retains all the factor sealed and with out extra exterior parts that may put on out or fail.
I used to be ready to take a look at a number of of those designs in Bafang’s showroom, and even examined them out later within the day on a number of totally different e-bikes sporting Bafang’s parts. However alas, I’m getting forward of myself.

A giant a part of R&D goes past simply imagining new parts. Bafang has to carefully check their designs to make sure they will deal with the cruel world through which e-bikes reside. From strain tanks of water that expose any air gaps in motors to brutal drop exams and shaker tables, the corporate’s engineers completely torture these poor units whereas in search of how and the place they will fail.
That testing not solely results in design enhancements, however typically even to the event of recent supplies. Bafang makes use of their very own proprietary materials for the gears used of their motors, providing extra power and ruggedness than typical nylon gears, however much less noise than metal gears.
There are soundproof rooms for making essentially the most minute measurements of the sounds produced by numerous parts, and even an EMC (electromagnetic compatibility) chamber for electrical security testing and compliance certification, the place e-bikes and parts may be examined to make sure that all the numerous items are working collectively correctly with out creating any pointless or probably problematic electromagnetic radiation. That is additionally important to making sure compatability of varied electrical parts in order that they don’t intrude with each other.
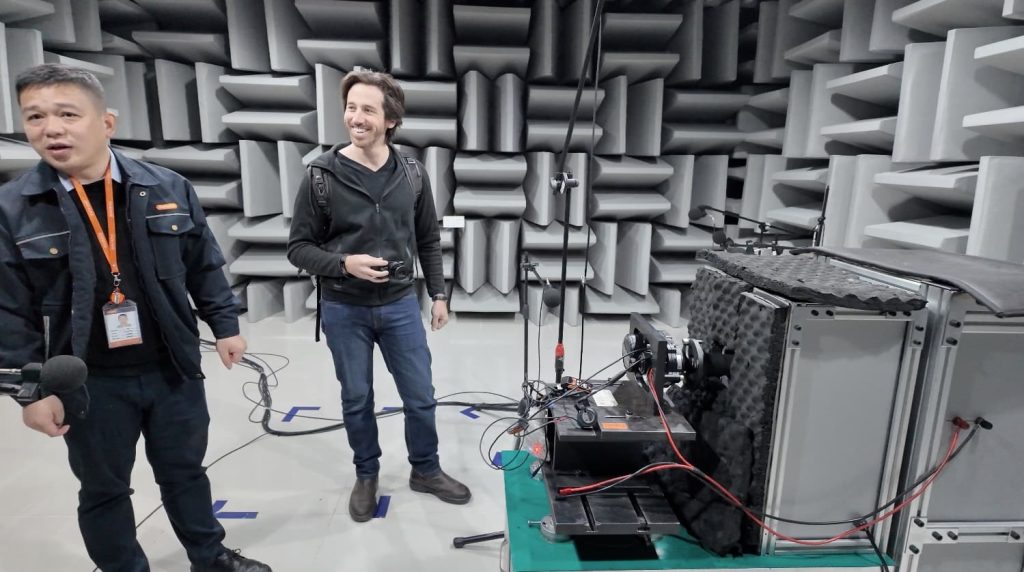
With a greater understanding of the method that goes into R&D, I moved on to the manufacturing facility the place manufacturing happens. Right here all of it begins in with high quality inspections that be certain that the parts that go into Bafang’s merchandise are inside manufacturing tolerances. Parts like motor shells and bearings are important to the efficiency of an e-bike’s drive system, and so parts are scrutinized in positive element with micron-level measurements earlier than they make it to the manufacturing facility ground the place they are going to be included into assemblies.
After passing their checks, parts head right into a largely automated course of. For instance, the motor shells are dealt with by robots that transfer them by means of a number of levels on an meeting line, including gears, spreading grease, and receiving their motor cores.
These motor cores cross by means of their very own robotic strains, with the copper wire spun by precision machines. One of these work was typically completed by hand years in the past, however has now been supplanted by automated machines which are quicker and extra correct.
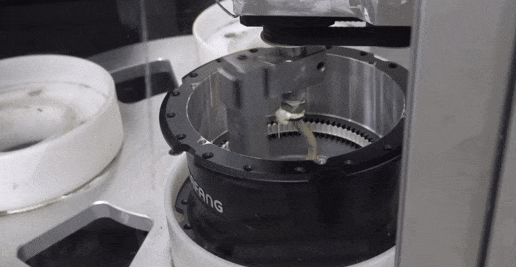
At this level, the sub-assemblies transfer to a ultimate meeting line, one of many few locations you continue to see numerous human employees. Right here, mid-drive motors obtain their ultimate meeting by hand. There are nonetheless a number of variations I seen although, akin to the shortage of laser-engraved serial numbers, which have now been changed by particular stickers that retain the motor shell’s corrosion-resistant end as a substitute of engraving it away. The one sticker additionally replaces the a number of stickers of varied styles and sizes that use to supply a hodgepodge of knowledge, and have now been streamlined right into a single unobstrusive marker that additionally leaves the protecting coating of the motor’s shell unaffected.
Motors are examined one ultimate time on a bench equipment, making certain they meet all the right specs, earlier than reaching their ultimate cease on the conveyor belt: packaging.
Close by, one other machine kinds small components akin to nuts and washers which are included with merchandise like hub motors, mechanically bagging them to be included within the motor packing containers.
It’s the same story for a number of different parts I noticed, from handlebar shows to wiring harnesses. A lot of the method has now been automated with particular machines that mechanically strip wires, mount connectors, glue show covers, and different steps which are extremely handbook and repetitive. Not every little thing has been changed by robots, and also you actually nonetheless see many line employees, however a big variety of the duties have been automated, and that looks like a pattern that can proceed.

One different intersting replace I noticed was a change to the best way the soldering stations are arrange. Beforehand, fumehoods have been mounted above soldering stations that may suck out the fumes from the soldering operations.
That helps stop these fumes from build up within the room, however the person employees at every sales space aren’t as protected for the reason that fumes nonetheless cross by their faces.
The brand new setup has vacuum holes within the precise workstation floor that suck the fumes down and out by means of the desk, stopping even the preliminary employee from being uncovered to soldering fumes.
It’s a nicer setup that protects everybody, and I used to be glad to see the upgrades.

Bafang Battery Manufacturing unit
The following a part of the tour took me into the battery manufacturing facility, which was like coming into a courageous new world for an e-bike components provider. Typically, battery factories are standalone operations run purely by battery makers. However Bafang has grown so giant that at this level, it is sensible for them to put money into constructing their very own top quality battery packs. It’s one thing they’ve been learning for almost a decade, principally staying within the R&D part. However in the previous couple of years, they’ve introduced these designs to life and entered full battery manufacturing.
Once more although, I’m getting forward of myself. Becuase it’s that design stage that’s important to the standard and security of batteries. Equally to the e-bike drive system aspect of issues, the battery manufacturing facility has its personal R&D part that scrutinizes totally different cells and batteries whereas getting ready and testing new designs to make sure they will meet the correct security and efficiency necessities set by Bafang. Assuming they do, they might find yourself slated for manufacturing and change into one of many firm’s new battery pack choices.
Manufacturing on the manufacturing facility ground begins with the person battery cells that can finally make up the bigger battery packs. They’re examined to make sure they cross high quality checks earlier than being mechanically sorted by robots into essentially the most acceptable mixtures of cells based mostly on related inside resistances.
Pc-controlled ultrasonic welding machines then mix these battery cells into bigger packs, that are encased in numerous enclosures relying on the particular mannequin of battery. Earlier than the battery circumstances are even sealed, every battery is put by means of a sequence of bench exams to make sure it meets the correct parameters. After the batteries cross these checks, they get sealed and despatched to carry out a whole testing cycle, the place rows of cabinets home a whole lot – perhaps 1000’s – of actively charging and discharging battery packs. After getting the inexperienced gentle following a profitable cost and discharge cycle check, the battery is lastly packaged and ready to be despatched on its method to an e-bike manufacturing facility.
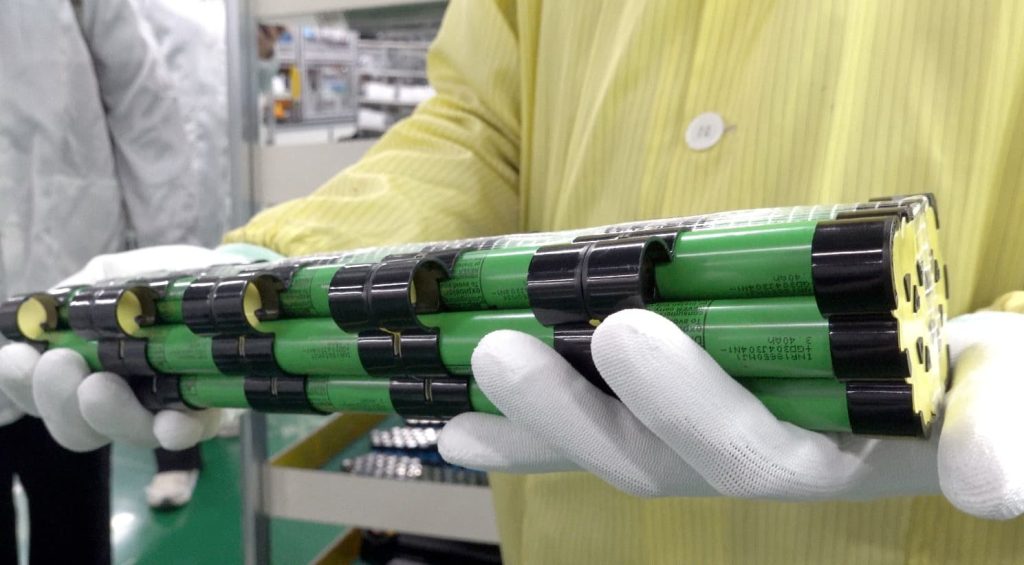


The dimensions of Bafang’s operations is nothing in need of spectacular. I’ve visited dozens of Chinese language factories at this level however I’ve by no means seen such an all-encompassing operation from an e-bike part maker. With the addition of battery packs, to not point out all the opposite drivetrain parts made by Bafang, the corporate really is a one-stop store now for e-bike OEMs.
It has been an unimaginable expertise to see not simply the parts and designs, however the best way that manufacturing has essentially modified within Bafang’s partitions during the last a number of years. And at this fee, I’m fascinated to see what new improvements the subsequent few years might deliver.
Don’t neglect to take a look at the video of this behind-the-scenes tour, under!
FTC: We use revenue incomes auto affiliate hyperlinks. Extra.